3D printers are useful devices for all kinds of reasons, but most have a critical weakness: they simply take a long time to actually make anything. That’s because additive manufacturing generally works by putting down an object one microscopic layer at a time. But a new holographic printing technique makes it possible to create the entire thing at once — in as little as a second or two.
Light-based 3D printing techniques generally use lasers to cause a layer of resin to harden in a pattern, but like extrusion printers, they have to do it layer by layer. If the laser shined all the way through the liquid resin, it would cause a big line of it to cure.
But what if you shined multiple weaker lasers through the resin, none of which was powerful enough to cure it except when they all intersected? That’s the technique developed by a team led by researchers at Lawrence Livermore National Laboratory.
This basic idea has been applied in several other domains: by carefully overlapping weak beams of light, sound or radiation, you can expose a chosen volume to a critical amount while leaving other areas largely untouched.
In this case, the three beams of light must be carefully patterned to only intersect with each other and produce that constructive interference in the exact points that need to solidify. And once that pattern is set, it only takes a handful of seconds to actually complete the process of curing the resin — drain it away and your object is ready to use. A couple of other techniques have attempted something like this, but haven’t been able to create complete 3D shapes like this.
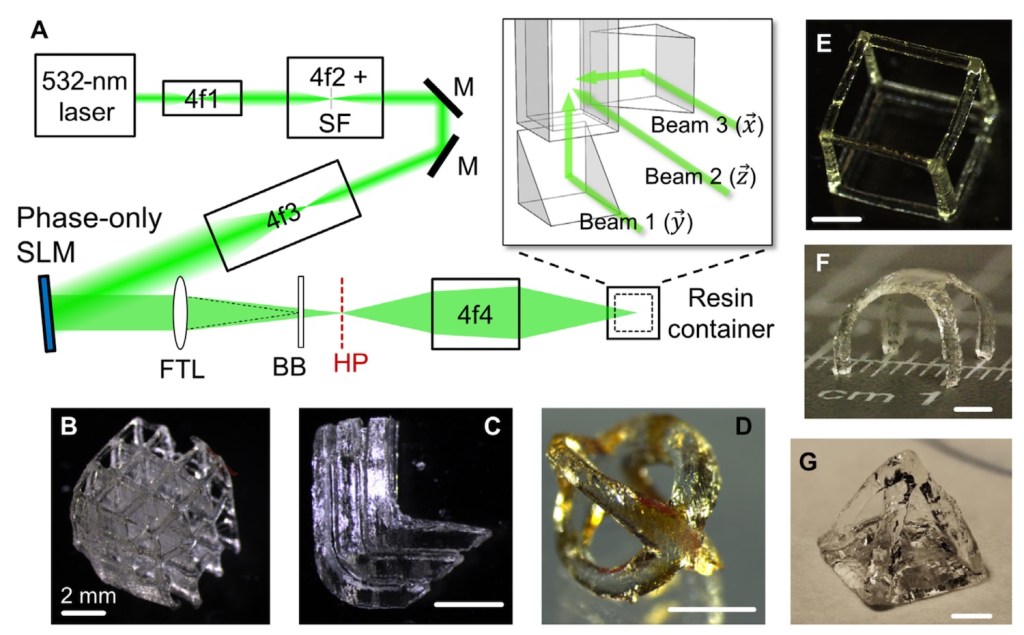
This figure from the paper shows the lensing and holographic setup as well as several examples of shapes printed using the technique.
The advantages are plenty: you could, for instance, produce structures with other structures freely moving inside of them, like gears in a gearbox. There’s no need for support structures underneath overhangs, so certain shapes that were impractical or impossible when printing from the bottom up or top down are straightforward to create this way. You also could quickly print multiple structures simultaneously — a bunch of dice, for instance.
It’s still a bit crude compared with what comes out of most commercial 3D printers, but that’s to be expected — this is really just a proof of concept in a lab.
“With this work we’ve taken a solid first shot at this to demonstrate and prove out that ‘3D all at once’ fabrication is possible,” lead researcher Maxim Shusteff told TechCrunch in an email. “So we haven’t yet pushed the limits of any of the build performance metrics (speed, build size, resolution, complexity).”
Ultimately the “resolution” will likely be determined by the smallest bit of resin that can reliably be solidified, which has to do with a number of chemical and optical factors. It would be premature to speculate on what that resolution might be, but from the results already obtained it seems clear that it will certainly work for the complexity levels for which 3D printers are already being used.
Shusteff and his colleagues at LLNL, MIT, Berkeley and the University of Rochester aim to continue to develop this highly promising technique. Commercial applications are still a ways away, but it’s not hard to imagine parties that would be interested in a 3D printer that creates things in a few seconds rather than, at the very least, several minutes, and more often, hours.
[“Source-techcrunch”]